Wire Harness vs. Cable Assembly: Navigating the Complexities
Written by Source Engineering | read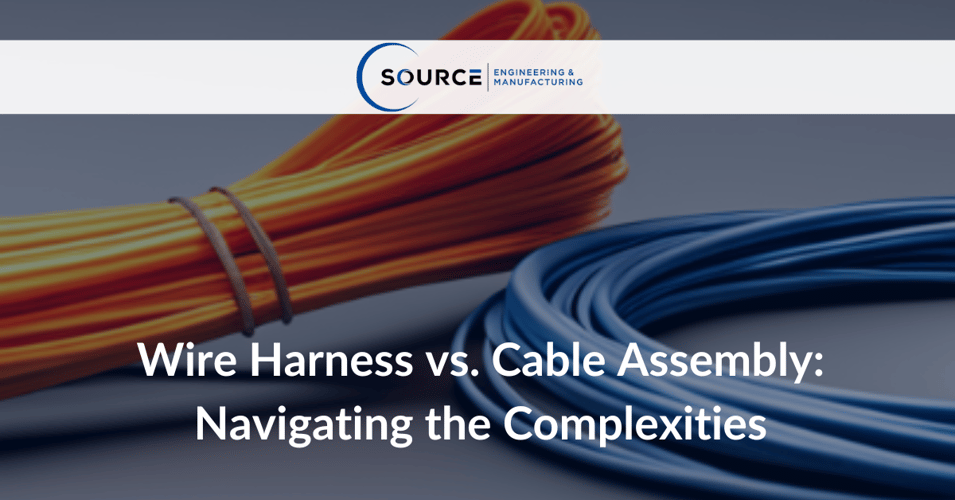
Table of Contents
In electrical systems, precision in choosing the right components can significantly influence functionality and efficiency. Two such critical components are wire harnesses and cable assemblies. Though they might seem similar at a glance, their applications, construction, and capabilities differ vastly. This article aims to demystify these differences, offering insights into their basics, manufacturing processes, and leading manufacturers to guide industry professionals in making informed decisions.
Understanding the nuances starts with defining what each component is. What is meant by a cable harness? Also known as a wire harness, it is an assembly of wires and/or cables that are bound together by straps, sleeves, cable ties, conduit, or a combination thereof, to form a single unit. These harnesses are designed to improve the organization of wiring systems by consolidating multiple wires into one sheath, reducing the space needed and protecting the wires from external abrasions, moisture, and other potential damages. This organization is critical in complex systems where hundreds or thousands of wires are present.
The primary distinction between these components revolves around their structure and complexity. What is the difference between wire and cable and harness? A single wire is a single conductor material, usually copper or aluminum, possibly insulated. A cable, on the other hand, is a group of wires sheathed together. A harness combines multiple cables or wires, routing them around a device or system to supply power and transmit signals. This brings us to what is the difference between a cable assembly and a harness? While both serve to organize wires, a cable assembly typically encases its components in a more robust outer sheath, designed for specific environmental conditions. It combines various types of cables and wires into a single, custom-designed connector assembly.
What is a cable harness specifically designed for encompasses more than just organizing and protecting cables. It is adeptly engineered to fit into spaces where it would be virtually impossible to fit individual wires and cables. Each configuration is carefully planned and laid out to meet specific requirements, considering factors such as electrical load, abrasion risk, and environmental conditions. This meticulous attention to detail ensures that wire harnesses not only enhance the safety of electrical systems but also improve their longevity and reliability.
What are the Basics of Wire Harness
At its core, a wire harness is designed for efficiency and organization. Utilizing various wiring harness materials such as PVC, rubber, or thermoplastic, manufacturers can ensure durability and resistance to environmental factors. Essential wire harness assembly tools play a pivotal role, including crimping tools, wire strippers, and heat-shrink tubing, facilitating a precise and reliable assembly process.
Selecting the right wire harness manufacturer hinges on their capability to provide high-quality, custom solutions. Source Engineering stands out in this regard, offering impeccable custom wire harnesses tailored to meet specific requirements, ensuring reliability and performance.
The cable assembly basics further delineate from wire harnesses in terms of complexity and design precision. Materials used in cable assemblies, such as high-grade thermoplastics or metals for the outer sheath, are selected based on the environmental challenges anticipated in their field of application. Advanced cable assembly equipment, including precision cutters, automated soldering stations, and environmental testing chambers, are essential for ensuring that each assembly meets the stringent requirements it faces. When considering a cable assembly manufacturer, one should evaluate their expertise in handling diverse material requirements, their ability to perform rigorous testing protocols, and their capacity for custom engineering solutions. In this context, Source Engineering also excels by providing adaptable, highly resilient cable assemblies that are engineered to perform under pressure, whether in critical healthcare devices, demanding industrial applications, or harsh outdoor settings.
Selecting the right partner for wire harness or cable assembly manufacturing is not just about comparing product specifications; it's about establishing a relationship with a provider that is committed to understanding and meeting your project's unique challenges. A customer-focused manufacturer like Source Engineering values collaboration, offering tailored advice and support from initial design through to final delivery. Their commitment to quality, combined with a deep understanding of both wire harness and cable assembly technologies, ensures that clients receive solutions that are not only technically sound but also optimized for their specific application. This approach provides an assurance of reliability and functionality that is indispensable in today’s rapidly evolving technological landscape.
What is the Process of Wiring Harness Manufacturing
The manufacturing of wire harnesses is a meticulous process involving several crucial steps. Initially, it starts with design and prototyping, where exact specifications are laid out. Following this, wires are cut and stripped, terminals are crimped, and assemblies occur. Quality control is paramount, with each harness tested for functionality and compliance.
Quality assurance in wire harness manufacturing is an area of utmost importance, requiring rigorous testing procedures to ensure each product meets the high standards expected by customers. This involves electrical, mechanical, and sometimes environmental tests designed to simulate the conditions the wire harness will face in its actual use. Such exhaustive testing protocols are critical in identifying any potential issues before the products are shipped, thereby reducing the risk of failures in the field. It's this dedication to quality that defines a reliable manufacturer, one that prioritizes the performance and dependability of its products above all.
Furthermore, the customization capabilities of a manufacturer play a significant role in the selection process. A provider that can offer bespoke solutions tailored to the specific needs of a project is invaluable. This level of service requires a deep understanding of the technical requirements, as well as a flexible manufacturing process capable of adapting to various design specifications. Whether it's a unique electrical load, specific resistance to environmental conditions, or unusual routing requirements, a manufacturer's ability to accommodate these custom needs is pivotal. This adaptability ensures that the final product not only fits the application perfectly but also performs reliably under the intended conditions.
What are the Basics of a Cable Assembly
A cable assembly is a group of wires or cables arranged into a single unit to transmit electrical power or signals efficiently. This arrangement is designed to simplify the installation process and improve the durability and performance of the cables by protecting against environmental factors, such as abrasion, moisture, and chemical exposure. The construction of a cable assembly involves the precise bundling of wires or cables, which are then encased in an exterior sheath. This sheath not only provides physical protection but also plays a crucial role in organizing the cables for specific applications, ranging from simple electronic devices to complex industrial machinery.
The choice between a custom cable assembly and an off-the-shelf cable assembly significantly impacts both the performance and integration of the assembly into the intended application. Custom cable assemblies are tailored to meet the exact specifications of a project, including specific lengths, connector types, and cable configurations. This customization allows for optimal performance in unique or demanding applications by addressing specific environmental conditions, spatial constraints, and electrical requirements. In contrast, off-the-shelf cable assemblies offer a convenient and often more cost-effective solution for standard applications, with the trade-off being a potential compromise in fit, function, and flexibility. The decision between custom and standard options ultimately depends on the project's unique requirements and constraints.
The technical sophistication involved in creating a custom cable assembly goes beyond mere physical construction. It encompasses a thorough understanding of electrical engineering principles to ensure optimal signal integrity and power efficiency. This includes careful selection of materials for each component of the assembly, from the conductor to the insulation and shielding materials, to match the electrical demands and environmental challenges of its application. For instance, the use of high-quality copper or aluminum conductors for optimal conductivity, coupled with advanced insulation materials like PTFE or PVC, provides resistance against high temperatures, abrasion, and chemical exposure. Additionally, shielding techniques such as braiding, wrapping, or foiling are employed to protect signal integrity against electromagnetic interference (EMI) and radio-frequency interference (RFI), which are critical considerations in environments where electrical noise can be detrimental to performance. This level of detailed engineering and material science knowledge is vital in designing and manufacturing cable assemblies that not only meet but exceed the rigorous demands of modern applications.
Who Makes the Best Wiring Harnesses
When it comes to identifying the best cable harness manufacturers and wire harness assembly companies, Source Engineering emerges as a leader. With over two decades of experience, a commitment to quality, and a focus on customer-specific solutions, our team ensures the highest standards are met. From custom cable assemblies to intricate wire harnesses and panel builds, our expertise is unparalleled.
Source Engineering specializes in servicing high-tech industries with low-volume, high-complexity needs, embodying the pinnacle of craftsmanship and technological prowess.
Conclusion
Choosing between a wire harness and a cable assembly depends on your project's specific requirements. Understanding the basics, manufacturing processes, and where to find the best manufacturers are crucial steps toward achieving optimal electrical system performance. Trust Source Engineering for your custom wiring solutions, where quality, reliability, and customer-focused service are at the heart of everything we do.