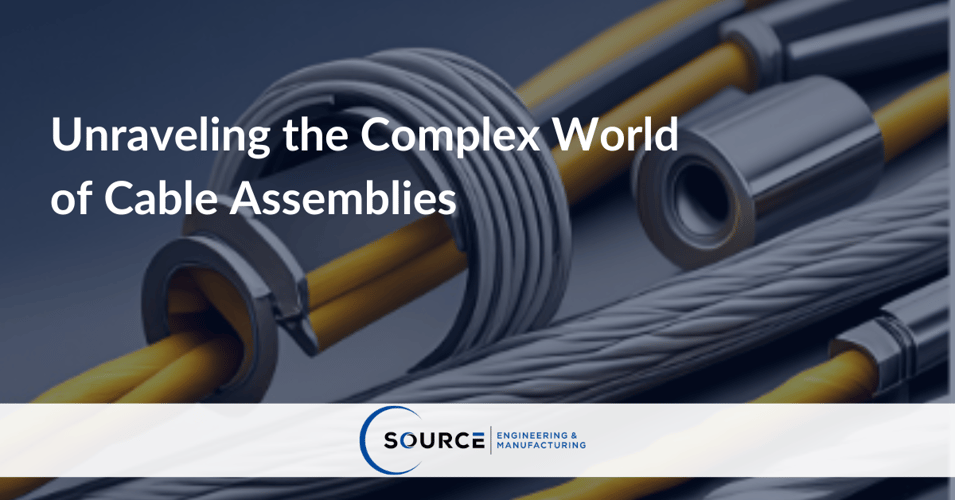
Table of Contents
Cable assemblies are integral components in various industries, serving as the backbone for numerous electrical systems. In this comprehensive guide, we will explore what cable assemblies are, their different types of applications, and how they differ from wire harnesses. With a focus on high-quality, custom solutions, we aim to provide you with a deep understanding of the critical role of cable assemblies.
At their core, cable assemblies consist of wires or cables systematically bundled together to efficiently transmit electrical signals or power from one point to another. These assemblies are meticulously designed and manufactured to withstand the specific environmental conditions they will be exposed to, such as extreme temperatures, vibrations, and moisture. This customization ensures that they meet the exact requirements of their application, offering reliability and high performance in even the most demanding situations. Whether for aerospace, automotive, medical, or telecommunications applications, our bespoke cable assemblies are engineered with precision, catering to the unique needs of each industry.
What is a Cable Assembly
Cable assemblies are complex groups of cables or wires that transmit signals or electrical power. They are designed with a protective outer layer to ensure durability and performance in harsh environments. This includes RF cable assemblies tailored for radio frequency transmission, Amphenol custom cables are known for their reliability, and a meticulous cable assembly process ensuring quality and precision.
Understanding the distinctions between different types of cable assemblies is essential for selecting the right solution for any given application. For instance, RF cable assemblies are designed to transmit radio frequency signals with minimal loss, making them ideal for telecommunications and broadcasting environments. In contrast, power cable assemblies are engineered to manage high voltage and current and are utilized extensively in the industrial and automotive sectors. Each type of cable assembly has its own set of characteristics, including impedance, maximum voltage rating, and environmental resistance, which must be carefully considered to ensure optimal performance and reliability.
The manufacturing process of cable assemblies involves several critical steps, each of which must be executed with precision to meet stringent quality standards. It begins with the design phase, where the specific requirements of the application are analyzed, and a blueprint is created. This is followed by the selection of materials, including the type of conductor, insulation, and protective jacket, which will determine the assembly's overall durability and performance. Subsequent steps include the precise cutting, stripping, and termination of cables, as well as rigorous testing to verify electrical functionality and durability under simulated environmental conditions.
For businesses looking for custom cable assembly solutions, it's essential to partner with a manufacturer that can produce assemblies to the exact specifications and one that adheres to the highest quality control measures. A reliable manufacturer will offer comprehensive services, from initial design consultation to prototyping and mass production, ensuring that the final product precisely meets your application's requirements. Furthermore, a customer-focused approach means that you receive ongoing support and the assurance that your cable assemblies will contribute to the longevity and efficiency of your electrical systems.
What are Cable Assemblies Used For
Cable assemblies are used in countless sectors, most notably by manufacturers developing specialized solutions for the automotive, aerospace, military, and telecommunications industries. Their design enables efficient and safe power and data transmission, underpinning the functionality of critical systems worldwide.
In the automotive industry, cable assemblies are fundamental in ensuring the reliable operation of vehicles' electrical systems. They are used in everything from the basic wiring of headlights and indicators to more complex systems like electronic stability control and infotainment systems. Automotive cable assemblies must adhere to strict standards for durability and performance, as they are subject to a wide range of environmental stresses, including thermal fluctuations, vibrations, and chemical exposures.
The aerospace sector relies heavily on cable assemblies for communication and navigational systems within aircraft. These assemblies must be lightweight yet robust enough to withstand extreme conditions, such as high altitudes, intense vibrations, and rapid temperature changes. The precision and reliability of these cable assemblies are critical, as any failure could have catastrophic consequences. Aerospace cable assemblies often incorporate advanced materials and technologies to meet these stringent requirements.
In telecommunications, cable assemblies are pivotal in transmitting data across vast distances. These assemblies ensure rapid and secure data transfer from the backbone networks that form the internet to the cables that connect cell towers. Telecommunications cable assemblies are specifically designed to minimize signal loss over long distances and, increasingly, to support the vast data requirements of 5G networks. Their design and manufacture require a profound understanding of electrical engineering and the specific needs of the telecommunications industry.
Cable assemblies are indispensable across various industries, including but not limited to:
- Automotive: Providing essential connections for vehicle electrical systems.
- Aerospace: Ensuring the reliability and functionality of aircraft communication and navigation systems.
- Medical: Connecting devices and instruments in critical healthcare applications.
- Telecommunications: Facilitating data transmission and communication infrastructure.
- Military: Offering durable and reliable solutions for defense technology.
- Industrial: Powering machinery and control systems in manufacturing and production environments.
- Capital Equipment OEMs: Partnering with original equipment manufacturers to supply tailored cable assemblies for complex machinery and large-scale industrial equipment, ensuring performance and safety standards are met.
- Consumer Electronics: Integrating components in a wide range of household devices.
Their versatility and adaptability make cable assemblies crucial in advancing technological innovation and efficiency across these sectors.
What is Flat Cable Assemblies
Flat cable assemblies are designed with a flat, rather than rounded, profile. This unique structure facilitates improved heat dissipation, ease of installation, and space savings. They're particularly favored in applications requiring dense wiring without sacrificing flexibility or performance.
The design of flat cable assemblies allows each conductor to lie in a single plane, significantly minimizing the cable thickness and weight. This characteristic is particularly beneficial in applications where space is at a premium, such as automotive dashboards or aerospace avionics, where the efficient utilization of space can directly impact overall system performance. Additionally, the flat form factor aids in enhancing airflow around the cables, which in turn helps in reducing overheating risks in tightly packed electronic assemblies. These assemblies often incorporate advanced insulation materials that contribute to the cable's slim profile and its high resistance against abrasion and environmental factors like moisture and chemicals.
Furthermore, the ease of installation and maintenance associated with flat cable assemblies is a noteworthy advantage. Their inherent design simplifies the routing and connection processes, enabling quicker assembly and potential cost savings on labor. These benefits are invaluable for industries where time and reliability are crucial, such as in medical or military applications. Flat cable assemblies also lend themselves to more straightforward diagnostics and repairs since their organized layout allows for easier identification of damage or wear. Recognizing these advantages, cable assembly manufacturers continue to innovate, pushing the boundaries of flat cable technology to meet the evolving demands of various industries.
What are Medical Cable Assemblies
Medical cable assemblies are specifically engineered to meet the stringent requirements of the healthcare industry. These assemblies must ensure reliability, sterility, and precision in applications ranging from surgical instruments to diagnostic devices, embodying a commitment to patient safety and care.
The significance of medical cable assemblies cannot be understated, as these components are integral to various medical devices, including imaging systems, patient monitors, and life support equipment. To meet the demands of these critical applications, medical cable assemblies are designed with a focus on durability, reliability, and biocompatibility. Materials used in these assemblies must not only withstand repeated sterilization processes but also be safe for direct patient contact. This requires the use of advanced materials that are resistant to chemicals, temperature extremes, and physical wear.
In addition to material considerations, medical cable assemblies are manufactured under strict quality control standards to ensure consistent performance and reliability. The precision in manufacturing is crucial, as any deviation can compromise the functionality of highly sensitive medical equipment. Manufacturers employ rigorous testing procedures to verify that their products meet both industry standards and specific customer requirements. This encompasses electrical, mechanical, and environmental testing to validate the durability and performance of the cable assemblies under various conditions.
Furthermore, the development of medical cable assemblies often involves close collaboration with medical device manufacturers to ensure that the assemblies are perfectly tailored to the specific needs of the device. This partnership is essential in addressing the unique challenges of medical applications, including the need for miniaturization, flexibility, and advanced functionality. By working directly with device manufacturers, cable assembly providers can create custom solutions that enhance the overall design and performance of medical equipment, thereby contributing to better patient outcomes and advancing healthcare technology.
What is the Purpose of a Cable Assembly
The primary purpose of a cable assembly is to consolidate multiple cables into a single, robust unit, facilitating easier installation and enhanced protection against environmental factors. This integration is crucial for maintaining the integrity and efficiency of electrical systems across various applications.
Cable assemblies play a pivotal role in ensuring the seamless operation and reliability of electronic and electrical systems. By combining multiple wires or cables into a single, cohesive unit, these assemblies provide a streamlined solution for power and signal transmission. This not only simplifies the design and installation process by reducing the clutter of individual cables but also significantly enhances system reliability. The bundled design of cable assemblies offers superior protection against external elements such as moisture, dust, and electromagnetic interference, which are critical factors in maintaining optimal performance in harsh or demanding environments. Furthermore, by customizing the length, connector types, and material composition of the cable assembly, engineers can optimize the assembly for specific applications, ensuring maximum efficiency and performance.
In industries where precision and durability are paramount, the quality of cable assemblies directly impacts the overall functionality and safety of the system. This is particularly evident in sectors like aerospace, automotive, and healthcare, where failure of a single component can have significant consequences. Manufacturers of cable assemblies recognize the critical nature of their products and adhere to stringent quality control measures during production. They utilize advanced manufacturing techniques and materials to meet the rigorous demands of their clients, ensuring that each cable assembly delivers reliable performance under the most challenging conditions. Additionally, the continued innovation in cable assembly technology addresses the evolving needs of these industries, including the demand for lighter, more compact, and more efficient assemblies. Through these efforts, cable assembly providers play an indispensable role in the advancement and reliability of modern technological systems.
What is the Difference Between Cable Assembly and Wire Harness
While both cable assemblies and wire harnesses are used to organize wires and cables, cable assemblies offer an additional layer of protection with a heavy-duty sheath, making them better suited for external or rugged applications. Wire harnesses, however, are typically used within enclosed spaces where less protection is required.
Choosing between a cable assembly and a wire harness depends on the specific requirements and constraints of the application. In environments where the cabling system is exposed to harsh conditions such as high temperatures, chemicals, or physical stress, a cable assembly is preferable. Its robust exterior sheath offers a higher level of protection, ensuring that the cables within maintain their integrity and performance over time. In contrast, wire harnesses are ideal for applications where space optimization and internal organization are key factors. Their simpler construction is designed for environments that pose fewer external threats, allowing for efficient routing and connection of cables within devices or machinery.
The design and customization of cable assemblies and wire harnesses are critical elements that significantly affect their functionality and compatibility with different applications. Manufacturers work closely with clients to understand their specific needs, including environmental conditions, space limitations, and electrical requirements. This collaborative approach ensures that the end product not only fits the physical dimensions of the space where it will be used but also meets the electrical specifications necessary for optimal performance. Customizations can include varying lengths, connector types, and wire gauges, as well as the integration of special materials or components to enhance the assembly or harness's resistance to specific environmental factors.
In the rapidly evolving landscape of technology and industry, the demand for both cable assemblies and wire harnesses continues to grow. Innovations in electronics, automotive technologies, aerospace, and healthcare devices drive the need for more sophisticated wiring solutions. As systems become more complex and the demand for reliability and efficiency increases, the role of these components becomes even more crucial. Manufacturers must stay ahead of these trends, investing in research and development to offer products that meet the advancing standards of these industries. This commitment to innovation and quality assures customers that they receive components that not only meet their current needs but are also forward-compatible with emerging technologies and challenges.
What is the Difference Between Wire and Cable and Harness
The difference lies in their construction and application. Wires are single conductors, cables are multiple conductors wrapped together, and harnesses are organized groups of wires or cables. Each serves a distinct purpose in transmitting power or signals within electrical systems.
Understanding these distinctions is integral to selecting the appropriate component for any given electrical system or application. For professionals in the field, correctly distinguishing between wire, cable, and harness can greatly affect the efficiency, safety, and cost-effectiveness of a project. Wires, being the most basic form of electrical conductors, are ideal for simple point-to-point connections. They are typically employed in applications where minimal external interference is expected, and the path of current flow is straightforward.
On the other hand, when multiple wires need to be organized and protected, cables serve as the preferred option. By grouping these conductors, cables minimize the space used and enhance the aesthetic and functional arrangement within devices. Furthermore, the additional layers of insulation and shielding materials in cables provide necessary protection against electrical interference, physical damage, and environmental factors, thereby ensuring that signals or power are transmitted reliably.
Harnesses, comprising organized cables or wires, embody the pinnacle of organization and protection in complex systems. They not only facilitate the neat arrangement and efficient connection of various components but also significantly ease installation and maintenance processes. By custom-tailoring wire and cable harnesses to the specific requirements of an application, including the integration of varying lengths, connector types, and protective sheathing, engineers can optimize electrical systems for performance while adhering to safety standards and regulatory requirements. This level of customization and consideration towards application-specific needs reinforces the reliability and functionality of the systems in which these components are integrated.
What are Custom Cable Assemblies
Custom cable assemblies are specialized solutions designed to meet the unique needs of clients across various industries. They involve the creation of a cable assembly that is tailored to the specific requirements of a project or application, considering factors such as the environmental conditions it will be exposed to, the electrical requirements it needs to meet, and the physical space it will occupy. This bespoke approach allows for enhancements in performance, durability, and compatibility, ensuring that the assembly works seamlessly within its intended application. Manufacturers of custom cable assemblies collaborate closely with their clients to understand these needs in detail, employing advanced manufacturing techniques and high-quality materials to produce components that meet precise specifications.
The advantage of opting for custom cable assemblies lies in their ability to solve complex challenges that off-the-shelf products cannot address. Whether it's a need for assemblies that can withstand extreme temperatures, corrosive chemicals, or rigorous physical stresses, a custom solution can be developed to overcome these obstacles. Furthermore, custom assemblies can integrate various types of connectors, specific wire gauges, and unique configurations that standard products do not offer. This level of customization not only ensures that the cable assembly will fit perfectly within its application but also enhances the overall performance and reliability of the system it is a part of. Through this tailored approach, customers receive a product that is not only fit for purpose but also contributes to the efficiency and longevity of their systems.
What is the Difference Between a Wire Assembly and a Cable Assembly
The key difference between a wire assembly and a cable assembly lies in their construction and protective covering. Cable assemblies are equipped with a more durable sheath, providing superior protection and making them ideal for challenging external or industrial environments compared to wire assemblies.
Choosing the right type of assembly for your project involves a thorough analysis of the operational environment, the nature of electrical signals involved, and the physical constraints of the application. Our team of experts specializes in assessing these factors, offering guidance to ensure that your choice between a wire assembly and a cable assembly aligns with your project's specific needs. This customer-focused approach not only guarantees the reliability and efficiency of the electrical systems but also contributes to the longevity and safety of the overall project.
In the dynamic field of electrical engineering and manufacturing, staying informed about the latest advancements and innovations is paramount. Our commitment to continuous improvement and staying abreast of industry trends means that we can offer state-of-the-art solutions to our clients. Whether it’s adopting new materials that enhance durability, or integrating the latest technology to improve performance, our dedication ensures that our clients receive products that are not just fit for purpose today but are also adaptable to the technologies of tomorrow.
Furthermore, our collaborative process doesn’t end with the delivery of your assembly; we provide comprehensive support throughout the lifecycle of the product. This includes technical support, maintenance advice, and any necessary upgrades to adapt to changing conditions or technological advancements. Our objective is to establish long-term relationships with our clients, based on trust, reliability, and a shared commitment to excellence in electrical engineering solutions.
What is a Cable Support System
A cable support system provides structural support to cables and assemblies, ensuring secure installation and organization. These systems prevent damage due to strain, environmental exposure, and other potential hazards, extending the lifespan and reliability of the cabling infrastructure.
Conclusion
Cable assemblies play a pivotal role in the functionality and reliability of modern electrical and electronic systems. Understanding their types, applications, and differences from similar components is crucial for selecting the right solution for your needs. Whether it's for medical, industrial, or any other application, custom cable assemblies offer tailored solutions that meet specific requirements with unmatched quality.
For those looking forward to exploring more about custom solutions for their next project, engaging with a seasoned manufacturer capable of delivering high-quality cable assemblies is essential. Contact us today to learn how our expertise can support your needs, ensuring the highest standards of performance and reliability for your systems.