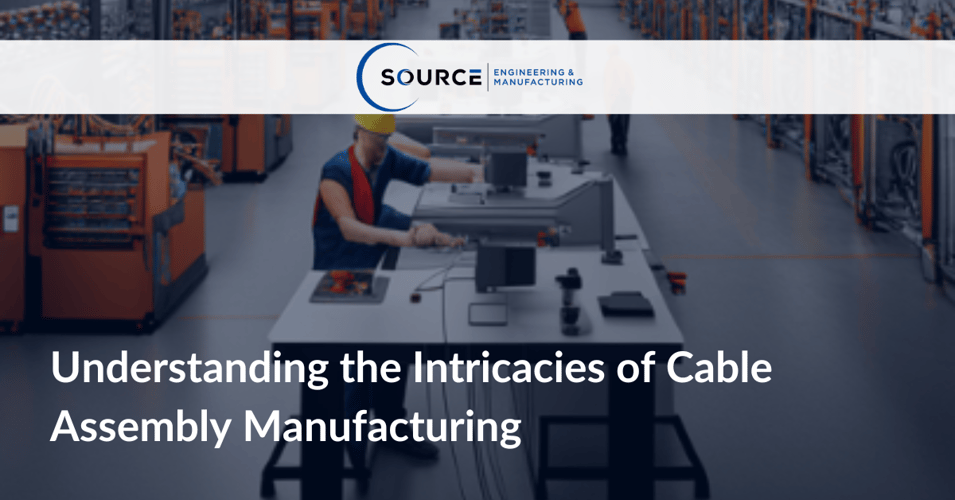
Table of Contents
The world of cable assembly manufacturing is a complex one, involving meticulous processes and diverse materials to ensure the production of high-quality cables suited for various applications. From the selection of raw materials to the intricate assembly process, every step is crucial in shaping the functionality and reliability of the final product. This article aims to demystify the cable assembly manufacturing process, providing insights into how cables are manufactured, custom cable assembly, and the importance of choosing the right manufacturer.
How Cables Are Manufactured
The manufacturing of cables involves several key stages, starting from the selection of material types to the formation of the cable itself.
Materials play a pivotal role in determining the quality and performance of the finished cable assemblies. Manufacturers choose materials based on the specific application requirements, including resistance to temperatures, chemicals, and physical wear. Conductors, insulation, and protective outer sheaths are selected with precision to ensure optimal functionality. The choice of copper for conductors is common due to its excellent electrical conductivity, whereas materials like PVC, polyethylene, and Teflon are favored for insulation and sheathing based on their protective qualities and durability.
The assembly process itself is a detailed operation that demands accuracy and expertise. It begins with the cutting and stripping of wires to precise lengths, followed by the soldering or crimping of connectors. In custom cable assembly, additional steps are incorporated to meet unique specifications, such as the integration of particular connectors, the inclusion of special protective sleeving, or the creation of cables that can withstand extreme environments. This level of customization requires a deep understanding of the application's demands and a flexible manufacturing process to accommodate them.
Cable Material Types
The choice of cable material plays a pivotal role in determining the cable's suitability for specific environments and applications. Materials range from copper, known for its excellent electrical conductivity, to fiber optics, which are essential for high-speed data transmission.
The selection of the appropriate cable material is further refined by considering environmental factors such as moisture, temperature extremes, and potential chemical exposure. For example, in marine applications where saltwater exposure is a concern, materials must be chosen for their corrosion resistance. Similarly, in industrial settings where cables are exposed to harsh chemicals or high temperatures, materials like Teflon, known for its high resistance to heat and chemicals, become the ideal choice. This meticulous attention to material selection ensures that the cable assembly can operate reliably under the specific conditions for which it was designed, underscoring the importance of a manufacturer's expertise in material science.
Furthermore, advances in cable manufacturing technology have expanded the possibilities for customization and efficiency in production. Manufacturers now employ sophisticated machinery that automates many of the processes involved in cable assembly, from wire cutting and stripping to the application of connectors. This automation not only increases the precision of the assemblies but also allows for higher production volumes, ensuring that customer demands are met promptly. Additionally, the use of advanced testing equipment ensures that each cable assembly meets the stringent quality standards required for its intended application, providing clients with assurance of reliability and performance.
Metal Wire Manufacturing Process
The process begins with the drawing of metal wires, typically copper or aluminum, to the desired thickness. This is followed by stranding, where multiple wires are twisted together to form a single conductor, enhancing the cable's flexibility and strength.
After the stranding process, the conductors undergo annealing, a heat treatment that softens the metal, enhancing its ductility and electrical conductivity. This step is crucial for ensuring that the wire can be flexibly used in various cable applications without compromising its strength or performance. The annealed wires are then cooled, further solidifying their structure to maintain the desired characteristics. Following annealing, these wires are often coated with an insulating material. This coating, which can range from simple plastics to more complex materials like Teflon for higher temperature resistance, serves multiple purposes. It primarily prevents electrical shorts by ensuring that wires do not come into direct contact with each other or with conductive materials. Additionally, this insulating layer provides physical protection against environmental factors, such as moisture, chemicals, and physical abrasion, further enhancing the cable’s durability and lifespan in diverse operating conditions.
The final step in the metal wire manufacturing process involves testing and quality assurance. Each batch of wires is subjected to rigorous electrical, mechanical, and environmental tests to ensure they meet the specific requirements for their intended use. Electrical testing verifies the wire's conductivity and resistance levels, ensuring they are within acceptable ranges for efficient performance. Mechanical tests assess the wire's tensile strength and flexibility, ensuring it can withstand the physical stresses it may encounter in application. Environmental testing simulates various conditions like extreme temperatures, humidity, and exposure to chemicals to guarantee the wire’s integrity and performance under such circumstances. Only after passing these stringent tests are the wires deemed ready for the next stage of cable assembly, underscoring the manufacturer’s commitment to producing reliable, high-quality products.
How Are Cables Formed?
Forming cables involves the assembly of these conductors, insulating them, and then encasing them in protective jackets. Insulation materials can vary based on the cable's application, with polyethylene and PVC being among the most common due to their durability and resistance to environmental factors.
Cable Jackets
The outermost layer, or jacket, of a cable, serves as a protective barrier against physical damage and environmental elements. Materials like PVC, rubber, and thermoplastic elastomers are frequently used for their resilience and protective properties.
When selecting materials for cable jackets, manufacturers must carefully consider the specific demands of the application environment. PVC, for instance, is highly favored for its excellent flexibility, electrical insulation, and resistance to fire, chemicals, and UV light, making it suitable for a wide range of indoor applications. In contrast, for cables that must endure more rigorous conditions, such as those used in outdoor, industrial, or marine environments, materials like thermoplastic elastomers (TPE) and rubber are preferred. These materials are chosen for their enhanced durability, superior resistance to extreme temperatures, and ability to withstand physical abrasions and various chemical exposures. The selection of these materials ensures the cable’s integrity and functionality over its intended lifespan, despite the challenging conditions it may encounter.
Furthermore, for applications requiring high levels of data transmission speed and integrity, such as in telecommunications or data centers, the choice of insulation material for the conductors is critical. Polyethylene (PE) and fluorinated ethylene propylene (FEP) are commonly used in these scenarios for their outstanding dielectric properties, which minimize signal loss and cross-talk between cables. FEP, in particular, exhibits excellent resistance to high temperatures and chemical attack, making it an ideal choice for plenum cable applications where fire resistance and low smoke production are essential. This careful selection of materials for both the insulation of conductors and the outer cable jackets exemplifies the manufacturer's commitment to delivering products that meet the highest standards of performance, safety, and reliability in any given application.
Raw Materials for Cable Manufacturing
The foundation of cable manufacturing rests on high-quality raw materials, including conductors (like copper or aluminum), insulation, and jacketing compounds, all selected based on the cable's intended use.
- Copper: Commonly used for its excellent electrical conductivity, making it ideal for conducting wires.
- Aluminum: Favored for its lightweight and good conductivity, often used in power transmission cables.
- Polyethylene (PE): A versatile insulation material known for its good dielectric properties.
- Polyvinyl Chloride (PVC): Widely used for insulation and jacketing, providing good flexibility and resistance to environmental factors.
- Thermoplastic Elastomers (TPE): Employed in harsh environments for their durability and resistance to extreme temperatures.
- Rubber: Offers superior flexibility and resistance to abrasions, suitable for heavy-duty cable applications.
- Fluorinated Ethylene Propylene (FEP): Used in high-performance cables for its excellent resistance to high temperatures and chemicals.
- Teflon: A specialized insulation material for high temperature and chemical resistance applications.
- Fiberglass: Sometimes used in high-temperature applications for insulation purposes.
- Kevlar: Added for strength and durability, often used in protective coverings to enhance the cable's tensile strength.
Custom Cable Assembly
Custom cable assembly is tailored to meet specific requirements, offering solutions that standard cables cannot.
Cable Assembly Process
This customized process involves designing and constructing cables to fit unique applications, considering factors like the type of connectors, the arrangement of wires, and the environmental conditions the cable will be exposed to.
In the realm of custom cable assembly, addressing client needs with precision and care is paramount. Our approach begins with a detailed consultation process, where we meticulously gather all necessary specifications directly from the client. This ensures that every aspect of the cable assembly is tailored to meet the distinct requirements of their application, from the selection of raw materials to the final design and layout of the assembly. Our commitment to customer satisfaction is reflected in our dedication to understanding and fulfilling their unique needs, whether it involves creating a cable for extreme environmental conditions, specific electrical performance criteria, or unique physical configurations.
Further solidifying our commitment to excellence, we employ the latest technology and techniques in the manufacturing process. Our skilled technicians utilize advanced equipment for cutting, stripping, soldering, and crimping to ensure each cable assembly is constructed to the highest standards of quality and reliability. Throughout the production process, rigorous quality control measures are in place to detect and rectify any discrepancies, ensuring that the final product not only meets but exceeds customer expectations. This customer-focused approach, combined with our technical expertise, enables us to deliver superior custom cable solutions that are reliable, durable, and perfectly matched to the specific demands of each application.
Cable Assembler Role
Cable assemblers play a critical role, meticulously constructing and testing each assembly to ensure it meets the required specifications and quality standards.
The role of a cable assembler is both intricate and fundamental in the production of custom cable solutions. These skilled professionals are responsible for the hands-on assembly of cables, following precise blueprints and specifications to construct products that meet exact client requirements. Their responsibilities extend beyond mere assembly; they are also tasked with conducting thorough inspections and functional tests on each cable product to ensure it adheres to strict quality and performance standards. Utilizing a combination of specialized tools and techniques, cable assemblers meticulously manage the soldering of connectors, the application of insulation, and the integration of protective jacketing, thereby playing a crucial role in the overall reliability and efficiency of the finished cable assemblies. This dedication to craftsmanship and quality control underscores the vital contribution of cable assemblers to the mission of delivering products that clients can depend on for their critical applications.
Applications of Cable Assembly
Custom cable assemblies find applications in a wide array of fields, including telecommunications, automotive, aerospace, and medical industries, underscoring their versatility and importance.
Custom cable assemblies are integral to the operation and success of various industries, each with its distinct requirements and challenges. Their applications include, but are not limited to:
- Telecommunications: For data transmission, infrastructure, and networking solutions.
- Automotive: In vehicles for wiring harnesses, sensors, and control systems.
- Aerospace: For communication systems, navigation controls, and power distribution.
- Medical: In diagnostic and therapeutic devices, patient monitoring systems, and imaging equipment.
- Industrial: For machinery control systems, robotic automation, and power supply.
- Energy: In renewable energy systems, power transmission, and distribution networks.
- Defense and Military: For communication devices, electronic warfare systems, and ruggedized equipment.
- Consumer Electronics: In devices such as smartphones, tablets, and home appliances for power and data transmission.
These applications highlight the critical role of custom cable assemblies in supporting the infrastructure and functionality of modern society across a broad spectrum of sectors.
Cable Harness Manufacturers
These manufacturers specialize in producing cable harnesses, which organize multiple wires into a single unit, simplifying installation and improving reliability and performance.
Cable harness manufacturers hold a pivotal role in the creation of complex cable assemblies that are essential for a multitude of applications across various industries. These entities are tasked with the design, engineering, and fabrication of cable harnesses, which involves the precise bundling of multiple cables and wires into a single, manageable unit. This bundling is critical for ensuring that the cable assembly can be installed efficiently, function correctly, and remain durable under the conditions it will face. Manufacturers must consider factors such as the electrical requirements, mechanical constraints, environmental exposures, and application-specific standards in their designs. Furthermore, they are responsible for integrating protective sleeving, securing elements, and connectors that are compatible with the end-use environment. Their expertise extends to the selection of materials and components that offer the necessary levels of performance, reliability, and safety, following rigorous industry standards and certifications. The meticulous process of cable harness manufacturing involves sophisticated techniques and machinery for precise cutting, stripping, routing, and wrapping of wires, along with thorough testing protocols to ensure the integrity and functionality of the harness. This thorough approach underscores the vital importance of cable harness manufacturers in ensuring the seamless operation and longevity of critical systems in diverse sectors.
Conclusion
The manufacturing of cables and cable assemblies is an intricate process that requires precision, expertise, and high-quality materials. Whether for general applications or specific, custom needs, selecting the right cable assembly manufacturer is crucial to ensuring the reliability and efficiency of your electronic and electrical systems. For those in need of custom cable assemblies, partnering with a reputable manufacturer can provide tailored solutions that meet and exceed expectations.
For more information on custom cable assembly solutions tailored to your needs, visit sourceeng.com.