How to Calculate Manufacturing Overhead: Practical Guide for Engineers
Written by Source Engineering | read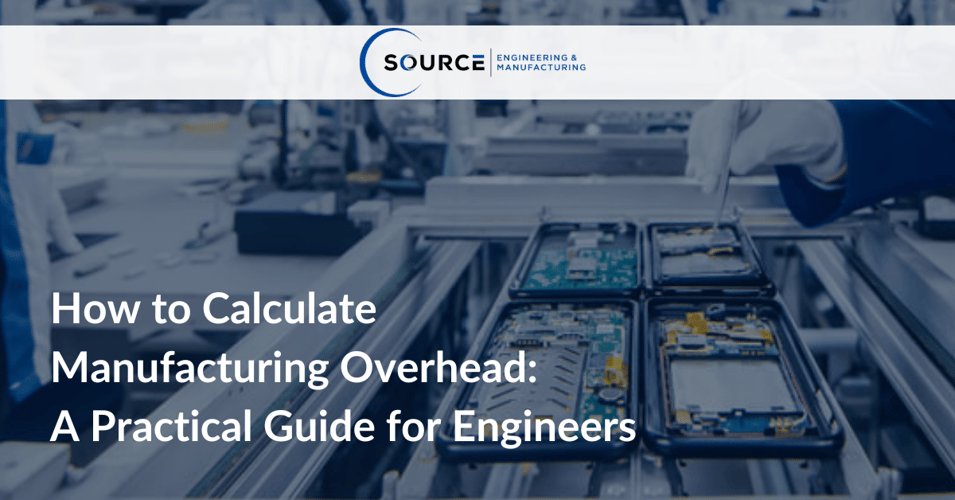
Table of Contents
For engineers and plant managers, managing costs is as vital as ensuring manufacturing efficiency. One of the most essential, yet often overlooked aspects of cost management is manufacturing overhead. Understanding and accurately calculating manufacturing overhead is critical for controlling budgets, setting competitive pricing, and improving overall operational performance in any industrial setup. This guide will walk you through what manufacturing overhead is, why it matters, and how to calculate it step-by-step. We'll also highlight common challenges engineers may face during this process and suggest solutions to overcome them.
What is Manufacturing Overhead?
Manufacturing overhead refers to all indirect costs that are a part of the manufacturing process but cannot be directly tied to producing a specific product. These are costs incurred to keep the facility operational and efficient. Overhead generally falls into three main categories:
1. Indirect LaborThese are wages paid to staff who do not directly work on products but are essential for operations, such as supervisors, maintenance technicians, and quality control personnel.
2. Indirect Materials
These include items like lubricants, cleaning supplies, and spare parts used during manufacturing but not directly included in the final product.
3. Other Indirect Costs
This can encompass utilities (electricity, water), depreciation of machinery, rent, facility maintenance, property taxes, and insurance premiums.
Why is Manufacturing Overhead Important for Engineers?
For engineers, especially those working in design, process optimization, or plant management, understanding manufacturing overhead offers several benefits:
- Accurate Cost Estimation
Knowing the total costs ensures that pricing is competitive and profitable. - Budgeting and Resource Optimization
It allows precise allocation of resources to reduce waste and streamline operations. - Identifying Hidden Costs
Overhead analysis can uncover inefficiencies, enabling engineers to devise strategies to minimize expenses. Now that we understand why overhead is critical, let's explore how to calculate it step-by-step. - Improved Decision-Making Understanding overhead helps in making informed decisions related to scaling operations or cutting unnecessary expenses.
- Enhanced Project Forecasting By accurately accounting for overhead, businesses can better predict the overall costs of future projects, improving planning and delivery.
- Competitive Advantage Managing overhead efficiently ensures that businesses can offer competitive pricing without compromising on quality.
- Financial Transparency A detailed understanding of overhead costs promotes clearer communication with stakeholders and aligns financial expectations.
Steps to Calculate Manufacturing Overhead
1. Identify All Indirect Costs
Start by gathering a comprehensive list of indirect costs incurred in the manufacturing process. This might include:
- Salaries for supervisors and quality control staff
- Utility bills (e.g., electricity for machines, HVAC systems)
- Depreciation on machinery
- Expenses for facility maintenance, rent, and insurance Practical Tip: Use software tools or resource planning systems to keep track of expenses in real time, reducing the risk of missing hidden costs.
2. Total the Indirect Costs
Once you've identified all indirect costs, add them up for a specific period—monthly, quarterly, or annually. For instance:
Expense Type |
Cost (Monthly) |
Supervisor Salaries |
$10,000 |
Utilities (Electricity) |
$15,000 |
Depreciation |
$5,000 |
Maintenance Supplies |
$2,000 |
Insurance and Taxes |
$3,000 |
Total |
$35,000 |
3. Determine the Overhead Rate
The overhead rate is the formula used to allocate overhead costs per unit of activity, such as direct labor hours or machine hours. The formula is: Overhead Rate = Total Overhead Costs ÷ Total Allocation Base
The "allocation base" depends on the nature of your manufacturing. For example:
- For labor-intensive setups, use direct labor hours.
- For machine-based industries, use machine hours. Example:
A CNC manufacturing unit incurs $100,000 in overhead costs and records 8,000 machine hours over a quarter. The overhead rate would be: Overhead Rate = $100,000 ÷ 8,000 machine hours = $12.50 per machine hour
4. Apply Overhead Costs to Products
With the overhead rate calculated, you can allocate costs to individual products. Multiply the overhead rate by the activity hours related to each product. Example:
If Product A requires 3 machine hours to manufacture:
Overhead Cost for Product A = 3 machine hours × $12.50 = $37.50 This ensures each product absorbs a fair share of overhead costs, giving you a clear picture of its total production cost.
5. Fine-Tune Calculations with Variable Variables
Adapt overhead calculations to suit your industry and equipment. For instance:
- Automotive sector: Focus on indirect costs like robotic maintenance or specialized tooling expenses.
- Pharmaceuticals: Factor in stringent facility upkeep and regulatory compliance costs.
- Small-scale workshops: Consider variable energy consumption or repair costs for custom machinery. Adding flexibility to calculations makes the data reliable across various engineering disciplines.
Common Challenges and Solutions
1. Hidden Indirect Costs
- Challenge: Costs such as minor repairs or upward utility rate changes often go unnoticed.
- Solution: Maintain a detailed ledger or invest in expense-tracking software that flags anomalies in overhead spending.
2. Allocating Costs Fairly
- Challenge: Engineering teams often struggle to decide on a fair allocation base.
- Solution: Evaluate historical data to identify whether direct labor or machine hours better reflect operational workloads.
3. Changing Production Volumes
- Challenge: Overhead rates may fluctuate with production levels, leading to uneven product pricing.
- Solution: Use flexible budgets that adjust rates based on production forecasts.
4. Maintaining Accuracy
- Challenge: Human errors during data collection can disrupt calculations.
- Solution: Where possible, automate data tracking and overhead allocation using advanced software solutions.
Visualizing Overhead for Better Understanding
Adding charts and graphs can simplify overhead calculations and help communicate costs effectively with teams. Here are some ideas:
1. Pie Chart of indirect costs (e.g., utilities, labor, taxes) to illustrate their proportions.2. Bar Graph showing total overhead costs over time to track trends and locate peaks. For example:
- Pie Chart Insight:
Utilities make up 40%, labor constitutes 30%, and depreciation covers 20% of your monthly overhead. - Bar Trend Example:
A spike in overhead costs during the summer signals increased air conditioning or equipment upgrades. Including such visuals helps improve clarity and strengthens decision-making.
- Line Graph Insight: A steady rise in sales from January to June followed by a plateau in summer could indicate seasonality in demand. This insight allows teams to plan inventory, staffing, and marketing campaigns more effectively. Identifying such trends ensures that resources are allocated efficiently and sales opportunities are maximized.
- Stacked Chart Insight: If online sales consistently make up 70% of total revenue while in-store sales cover just 30%, focusing on improving the digital customer experience could yield the best returns. By breaking down revenue sources, businesses can prioritize areas with the most potential for growth or identify underperforming segments.
- Scatter Plot Insight: Analyzing the relationship between marketing spend and customer acquisition rates could reveal diminishing returns at certain spending levels. This insight helps in setting optimal budgets to maximize impact without excessive costs.
Combining these visual tools ensures that data is not only presented clearly but also contextually analyzed, enabling smarter, evidence-based decision-making. Each graph or chart delivers unique insights that can guide different aspects of strategy, operations, and planning, fostering a comprehensive understanding of the business landscape.
Conclusion
Accurate manufacturing overhead calculations are the backbone of efficient production cost management. For engineers, assessing overhead costs ensures better pricing strategies, detailed budget planning, and operational clarity. By following the steps outlined here, engineers across industries can achieve more streamlined and profitable operations.